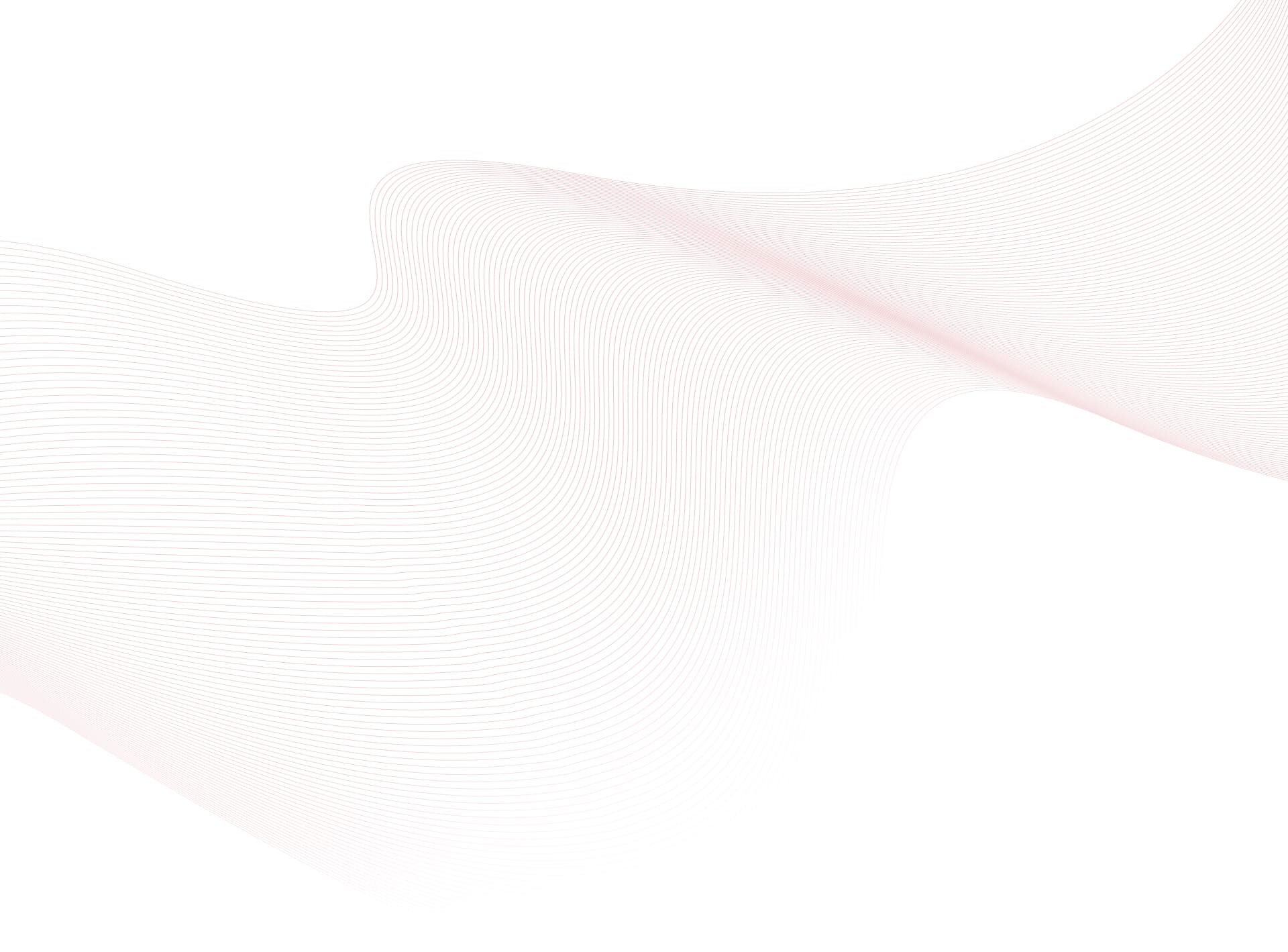
- Product Description
- Product Feature
- Product Specification
The extrusion line has maximum PP melting output. Capacity is 160 ~ 520 kg/h and the unit is equipped with a screen filter changer and rotary blade slitting system. The machine has less down time and prevents production loss. The pressure rollers of the take-off unit are pneumatically controlled, and have synchronized control electronic system. European gearbox, static mixer, screen filter changer, inverter, electrical part, etc... and human machinery interface & tape fibrillator device are available to meet special requirements.
Raffia tape stretching line is designed for producing PP/HDPE raffia tape and flat yarn which used for woven bag, geotextile, artificial grass, carpet backing production, and more. Capacity is 160-520 kg/hr,and the unit is equipped with a belt type screen filter changer and rotary type slitting unit for none stop operation.
The tape plant has low energy consumption, less down time and reduces production loss. The pressure roller of the equipment are pneumatic controlled, and have one-step synchronize control electronic system. The machine can incorporate with European-made gearbox, T-die, melt pump, tape winder upon customer's special requirement. Designed for making 500-1500 denier (2000-6000 denier upon special request).Working speed from 100-270 meter/minute.
![]() |
![]() |
![]() |
![]() |
![]() |
![]() |
![]() |
- Touch screen interface.
- Chiller.
- Air Conditioning unit for electrical cabinet.
- Static mixer unit.
- Dosing system.
- Tape fibrillation device.
- The T-Die gap is adjustable.
- Suitable for extruding PP and HDPE.
- The screw and barrel are manufactured from SCM-1 alloy steel, nitrogen treated and precision ground.
- Gears inside the gearbox are precision ground for noise-free cooling the oil of the gearbox.
- Built with auto loader and patent design material force feeding unit.
- Choice of AC or DC motor drive.
- Low energy consumption.
- Constructed with 1~6 rows of slitting blades.
- The slitting width is adjustable.
- Full pneumatic operation for convenience.
- Fitted with edge trim auto - recycle unit.
- Two stages hot air circulation system ensures raffia tape proper stretched.
- Air flow volume is adjustable.
- Exclusive 2 independent driving motors provides raffia tape with superior quality.
- Static electricity elimination provided.
- Waste yarn collection box for reclaiming is provided.
- Electronically controlled yam tension.
- Magnetic disk tension control available.
- Tape fibrillation device(optional)
HY7/SP-80HE | HY7/SP-90HE | HY7/SP-100HE | HY7/SP-110HE | HY7/SP-120HE | ||
---|---|---|---|---|---|---|
Extruder | Screw diameter | 80 mm | 90 mm | 100 mm | 110 mm | 120 mm |
Screw L/D | 30/1 | 30/1 | 30/1 | 30/1 | 30/1 | |
Screw material | SCM-1 | SCM-1 | SCM-1 | SCM-1 | SCM-1 | |
Cylinder material | SCM-1 | SCM-1 | SCM-1 | SCM-1 | SCM-1 | |
Maximum PP melting output | 160 kg/h | 240 kg/h | 320 kg/h | 420 kg/h | 520 kg/h | |
Maximum HDPE melting output | 120 kg/h | 170 kg/h | 240 kg/h | 320 kg/h | 410 kg/h | |
T-DIE | T die width | 650 mm | 900 mm | 1150 mm | 1350 mm | 1700 mm |
Film width | 550 mm | 800 mm | 1050 mm | 1250 mm | 1600 mm | |
Number of flat yarn | Upto 110 pcs | Upto 150 pcs | Upto 200 pcs | Upto 240 pcs | Upto 310 pcs | |
Die gap application | Adjustable | Adjustable | Adjustable | Adjustable | Adjustable | |
Control Panel | Type | Single type controller box | Single type controller box | Single type controller box | Single type controller box | Single type controller box |
Temperature controller | 10 zones | 12 zones | 14 zones | 15 zones | 17 zones | |
Cooling Device | Cooling method | Water circulation | Water circulation | Water circulation | Water circulation | Water circulation |
Quench system | Water bath system | Water bath system | Water bath system | Water bath system | Water bath system | |
Take-Off Unit A | Take off roller | 190 x 700mm x 2pcs | 190 x 950mm x 2pcs | 190 x 1200mm x 2pcs | 190 x 1400mm x 2pcs | 190 x 1700mm x 2pcs |
Powerful water suction unit | Equipped | Equipped | Equipped | Equipped | Equipped | |
Three wheel type stretching unit | ||||||
a) Edge trim auto recycle unit | 1 set | 1 set | 1 set | 1 set | 1 set | |
b) Press roller | 190 x 700mm x 3pcs | 190 x 950mm x 3pcs | 190 x 1200mm x 3pcs | 190 x 1400mm x 3pcs | 190 x 1700mm x 3pcs | |
c) Included 1 pc of rubber pressing roller | ||||||
R.P.M. Display | 0 - 60 m/min | 0 - 60 m/min | 0 - 60 m/min | 0 - 60 m/min | 0 - 60 m/min | |
Rotary tape slitting unit | Equipped | Equipped | Equipped | Equipped | Equipped | |
Edge trim auto recycle unit | Equipped | Equipped | Equipped | Equipped | Equipped | |
Stretching Device | Type | Oven (Hot air circulation) | Oven (Hot air circulation) | Oven (Hot air circulation) | Oven (Hot air circulation) | Oven (Hot air circulation) |
Take-Off Unit B and Annealing (Relaxation) | Take off godet | 7 pcs | 7 pcs | 7 pcs | 7 pcs | 7 pcs |
Pneumatic type press roller | 1 PC | 1 PC | 1 PC | 1 PC | 1 PC | |
a) First 4 stretching godets including Heating plate | 1 set | 1 set | 1 set | 1 set | 1 set | |
b) Last 3 annealing godets including Chill roller | 2 pcs | 2 pcs | 2 pcs | 2 pcs | 2 pcs | |
R.P.M. display | 0 - 320 m/min | 0 - 320 m/min | 0 - 320 m/min | 0 - 320 m/min | 0 - 320 m/min | |
Static electricity eliminator | Equipped | Equipped | Equipped | Equipped | Equipped | |
Waste yarn collector | Equipped | Equipped | Equipped | Equipped | Equipped | |
Winding Machine (With Synchronized Control) | Number of winder | 110 pcs | 150 pcs | 200 pcs | 240 pcs | 310 pcs |
Flat yarn wind-up roll | 150 x 200 mm (L) | 150 x 200 mm (L) | 150 x 200 mm (L) | 160 x 200 mm (L) | 150 x 200 mm (L) | |
Maximum mechanical winding speed | 320 m/min | 320 m/min | 320 m/min | 320 m/min | 320 m/min | |
General | Tape line speed | 270 m/min | 270 m/min | 270 m/min | 270 m/min | 270 m/min |
Denier application | 500 - 1500 | 500 - 1500 | 500 - 1500 | 500 - 1500 | 500 - 1500 | |
Total start-up power | 250 HP | 310 HP | 390 HP | 410 HP | 480 HP |